Organic impurities clay and other fine material :- This test is an approximate method for estimating whether organic compounds are present in the natural sand in an objectionable quantity or within the permissible limit.
The sand from the natural source is tested as delivered and without drying. A 350 ml graduated clear glass bottle is filled to the 75 ml mark with 3 percent solution of sodium hydroxide in water. The sand is added gradually until the volume measured by the sand layer is 125 ml.
The volume is then made up to 200 ml by adding more solution. The bottle is then stoppered and shaken vigorously. Roding also may be permitted to dislodge any organic matter adhering to the natural sand by using glass rod. The liquid is then allowed to stand for 24 hours. The colour of this liquid after 24 hours is compared with a standard solution freshly prepared, as follows:
Add 2.5 ml of 2 percent solution of tannic acid in 10 percent alcohol, to 97.5 ml of a 3 percent sodium hydroxide solution. Place in a 350 ml. bottle, stopper, shake vigorously and allow to stand for 24 hours before comparison with the solution above and described in the preceding paragraph. Alternatively, an instrument or colouredacetate sheets for making the comparison or coloured acetate sheets for making the comparison can be obtained, but it is desirable that these should be verified on receipt by comparison with the standard solution.
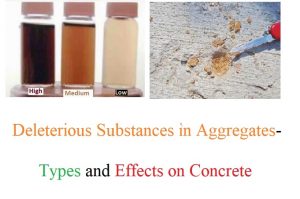
Water quality of mixing of concrete :- For proper chemical reaction, the amount of water required is about 25% of weight of cement, however more water is used for proper workability of concrete. The water used for mixing should be free from injurious amount of oils, acids, alkali, salts, organic materials or other substances that may be harmful to concrete on reinforcing steel.
Potable water is considered satisfactory for mixing concrete Water is used in accordance to IS 3025 – 1984 to 1988 (part 1 -32) To find out whether a particular source of water is suitable for concrete making or not, is to make concrete with this water and compare its 7 days and 28 days strength with comparison cubes made with distilled water.
If compressive strength is upto 90%, the source of water may be accepted. This criteria can be safely adopted in place like coastal area or marshy area or in other places where the available water is brackish in nature.
Seawater chloride content :-Sea water has a salinity of about 35 percent. It is reported that the use of sea water for mixing concrete does not appreciably reduce the strength of concrete although it may lead to corrosion of reinforcement in certain cases:
Research workers are unanimous in their opinion, that sea water can be used in un – reinforced concrete or mass concrete. Sea water slightly accelerates the setting time of cement. It also slightly accelerates the carly strength time of cement. It also slightly accelerates the carly strength of concrete.
But it reduces the 28 days strength of concrete by about 10 to 15 percent. However, this loss of strength could be made up by redesigning the mix. Water containing large quantities of chlorides in sea water may cause efflorescence and persistent dampness.
When the appearance of concrete is important sea water may be avoided. The use of sea water is also not advisable for plastering purpose which is subsequently going to be painted.
For economical or other pressing reasons, if sea water cannot be avoided for making reinforced concrete, particular precautions should be taken to make the concrete dense by using low water cement ratio coupled with vibration and to give an adequate cover of at least 7.5 cm. T
he use of sea water must be avoided in prestressed concrete work because of stress corrosion and undue loss of cross section of small diameter wires.